Hello,我是极速拍档的二·七,在2019年中国保险汽车安全指数,也就是我们俗称的中保研碰撞测试中,我发现了一个有趣的事情。某些车型国内版的碰撞测试成绩,跟海外版的碰撞测试成绩相去甚远。
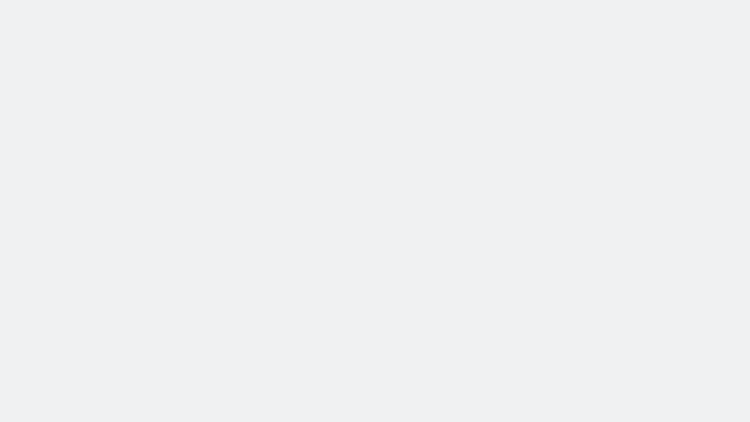
于是我翻了一下中保研碰撞测试,并且跟海外版的车型作对比,发现国内版与海外版本有差别的情况不在少数。为什么他们会有这样的差异?正好最近收到广丰的邀请去参观他们的南沙工厂,也许通过参观广丰的工厂,我能够找到答案。
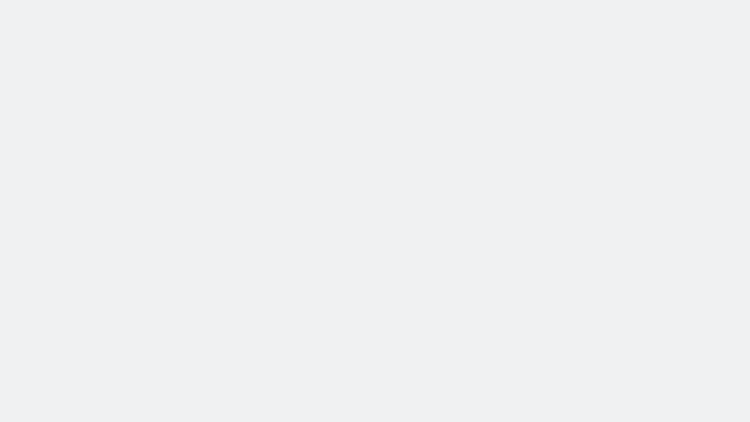
TNGA的全称是Toyota New Global Architecture,翻译过来就是“丰田新全球架构”。在2010年丰田正式提出了这个概念,TNGA不是一个特殊的平台,而是丰田一个全新的全球生产体系架构,甚至可以说是丰田生产理念的一种转变。
在2010年往后推出的丰田车型,全都基于这一个生产体系架构来研发、生产。
在导入TNGA之前,产品开发的过程,各个环节的管理者都是各司其职,而且零件是以车型轴设计开发的,不同车型会进行不同的开发。这就会导致各个系统之间的匹配出现问题。
这就有点像大学的食堂,采购食材的只管买菜,厨师只负责炒菜,盛菜的阿姨也只管把食物卖给我们。如果我们发现菜不好吃,或不新鲜,再一层层找原因,找到最后才发现,哦,是因为厨师要的食材没买,无奈只能换个方法煮,结果就造成菜不好吃了。
而在导入之后,车辆开发是以车型轴和零部件轴设计共同进行的,在设计、生产技术、制造管理这三大环节的管理人员是全程管理、同步开发的,这就能在各个系统之间的匹配做出优化调整。
这就好比食堂买菜的阿叔,买菜前会跟大厨商量今天需要的材料,大厨在炒菜过程中盛菜的阿姨会帮忙试味道,试吃没问题再卖给学生,卖完之后还会及时收集同学的意见,再跟采购和厨师反馈,这样操作下来食堂的饭菜质量应该也不止提升一个等级吧。过去丰田采用的是固定吊顶式,这种生产线容易受建筑结构的影响,一旦安装好便很难改变。而在新架构下,则换用了地面轨道式,它有点像火车的轨道。如果要增产,只要在原有的轨道上延长就可以了。也就是说,生产线能因应不同车型,随时切换模式实现共线生产。另外在制造环节,丰田引入“自工序完结”的检测方式。它的原理是:在生产前先将前期设计的标准全部输入到机器里面,然后机器就会在生产的同时又能检测产品是否达标。
这样就不用等到生产完成之后再进行检查,所以零部件的合格率提升了,而零部件合格率又去提升推动了丰田在整车一次组装合格率方面的提升。
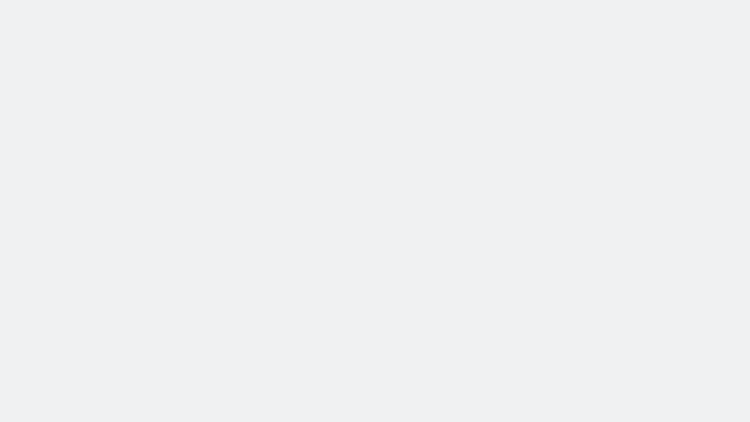
首先是车身结构,以全新雷凌为例,整体车身采用大量高强度钢,并且使用高压焊枪打点,以及车身结构的优化,使车身的整体刚性相比之前提升了37%。
第二,TNGA带来生产上流程的变化,以及由于TNGA共线生产的特性,TNGA下的车辆都有共通性,也就是说它们能够使用大量通用化的零部件,也就是说低等级的车也能与高一级的车用相同品质的基础零件。所以无论这台丰田售价高或低,它们在车身结构的安全性方面都不会有翻天覆地的差别。当然在某些配置上的差距还是有的,比如气囊的数量以及主动刹车之类的主动安全系统,高级别的车肯定会更丰富,不然也不会有人多花钱去买更高级别的车了。
第三,由于“自工序完结”的检测方式,这样就不用等到生产完成之后再进行检查,所以零部件的合格率提升了,而零部件合格率又去提升推动了丰田在整车一次组装合格率方面的提升。
换句话来说就是:由于零部件不合格导致的不安全事件概率更低了。
回到刚开始提出的问题:为什么国内版与海外版本的碰撞成绩会有差异?之所以在开头我要谈TNGA,是因为丰田在TNGA的引入后,丰田在整个生产流程、生产线以及车身材料上都有巨大的提升。并且由于TNGA的global(全球)理念,这些提升是海内外都同步的,所以国内外版本雷凌在安全性上的差异,并不太大。这也给我们一个思考:一台车的全球化并不仅在于美国有这台车、欧洲有这台车、中国也有这台车,更重要的是它们在生产上做到统一,而且是统一的安全。中保研这样的国内碰撞测试机构的诞生,也能促使全球所有厂家都能按照全球统一标准去生产车,因为安全是普通消费者买车最重要的考量标准之一。而在中保研这样的机构的监督下,消费者才有一个可量化的标准来看到差异,才能越来越减少各大厂家海内外版本“双标”的情况发生。